Introduction
3D printing, also known as additive manufacturing, has revolutionized the way we design, prototype, and manufacture objects. From intricate aerospace components to personalized medical implants, the technology has opened new frontiers across industries. At its core, 3D printing builds three-dimensional objects layer by layer, based on digital models. This article dives deep into 3D printing technologies and explains the technical processes that make it all possible.
What Is 3D Printing?
3D printing is a manufacturing process where material is added together (rather than removed, as in traditional machining) to create a three-dimensional object. A digital 3D model, usually designed using Computer-Aided Design (CAD) software, guides the printer in depositing material precisely where it’s needed.
Depending on the specific technology and material used, the process can involve melting, sintering, curing, or bonding particles together.
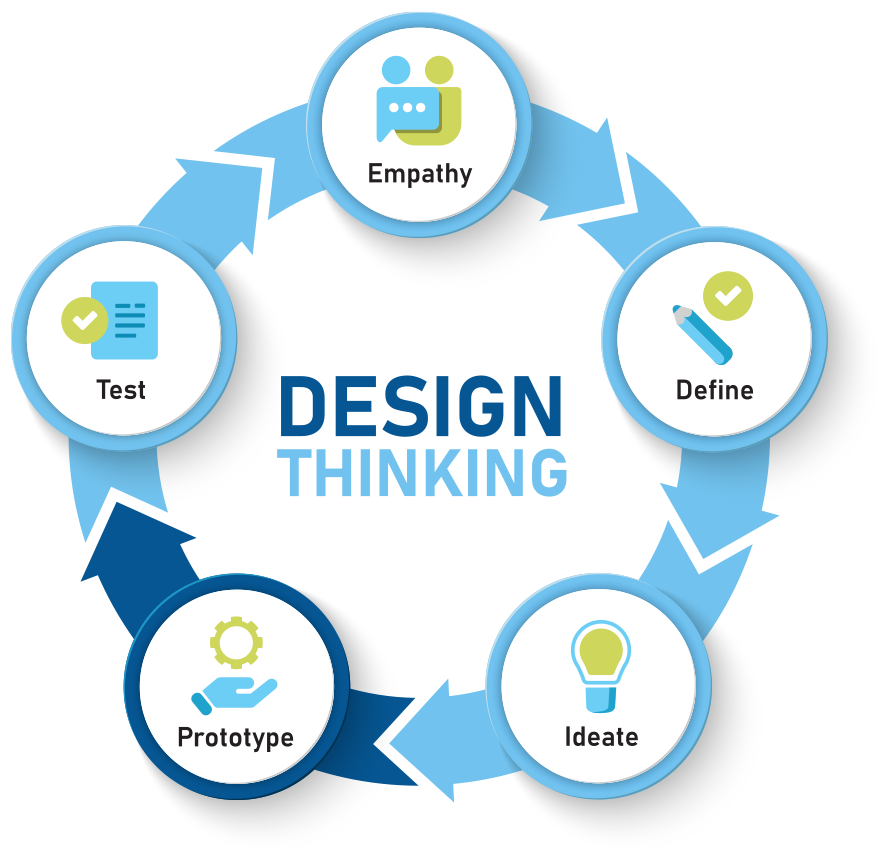
Key 3D Printing Technologies
Several types of 3D printing technologies exist, each suited to different applications:
1. Fused Deposition Modeling (FDM)
Process:
- Material: Thermoplastic filament (e.g., PLA, ABS)
- The filament is fed through a heated nozzle, melted, and extruded layer by layer onto a build platform.
- The nozzle moves according to the digital design, creating the object from the bottom up.
Advantages:
- Cost-effective
- Wide material selection
- Simple and accessible for beginners
2. Stereolithography (SLA)
Process:
- Material: Liquid photopolymer resin
- A UV laser selectively cures (hardens) the resin layer by layer.
- Once a layer is solidified, the build platform moves down (or up, depending on printer design) and the next layer is cured.
Advantages:
- High precision and smooth surface finish
- Excellent for detailed prototypes
3. Selective Laser Sintering (SLS)
Process:
- Material: Powdered polymer (e.g., nylon)
- A laser selectively fuses (sinters) powder particles together layer by layer.
- After a layer is complete, a new layer of powder is spread over the bed, and the process repeats.
Advantages:
- Strong, functional parts
- No need for support structures (powder acts as a support)
- Great for complex geometries
4. Direct Metal Laser Sintering (DMLS) / Selective Laser Melting (SLM)
Process:
- Material: Metal powders (e.g., titanium, aluminum)
- A laser melts (SLM) or sinters (DMLS) the metal powder into solid structures layer by layer.
Advantages:
- Production of fully dense metal parts
- Critical for aerospace, automotive, and medical implants
Technical Process of 3D Printing: Step-by-Step
While different technologies vary in method, the general workflow of 3D printing follows these common steps:
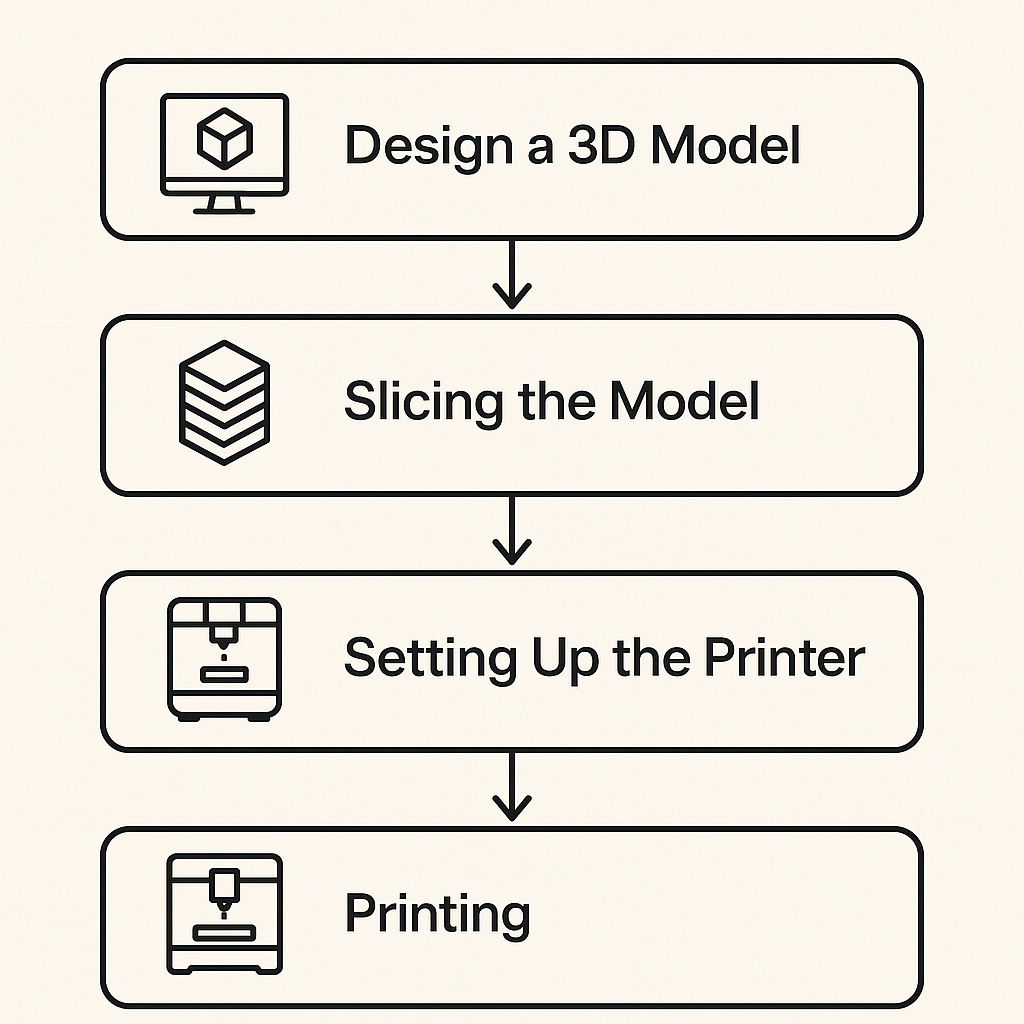
Step 1: Design a 3D Model
- Use CAD software (e.g., SolidWorks, Fusion 360) to create a digital model.
- Models must be watertight (no holes) and printable.
- The design is exported as an STL (Standard Tessellation Language) or OBJ file.
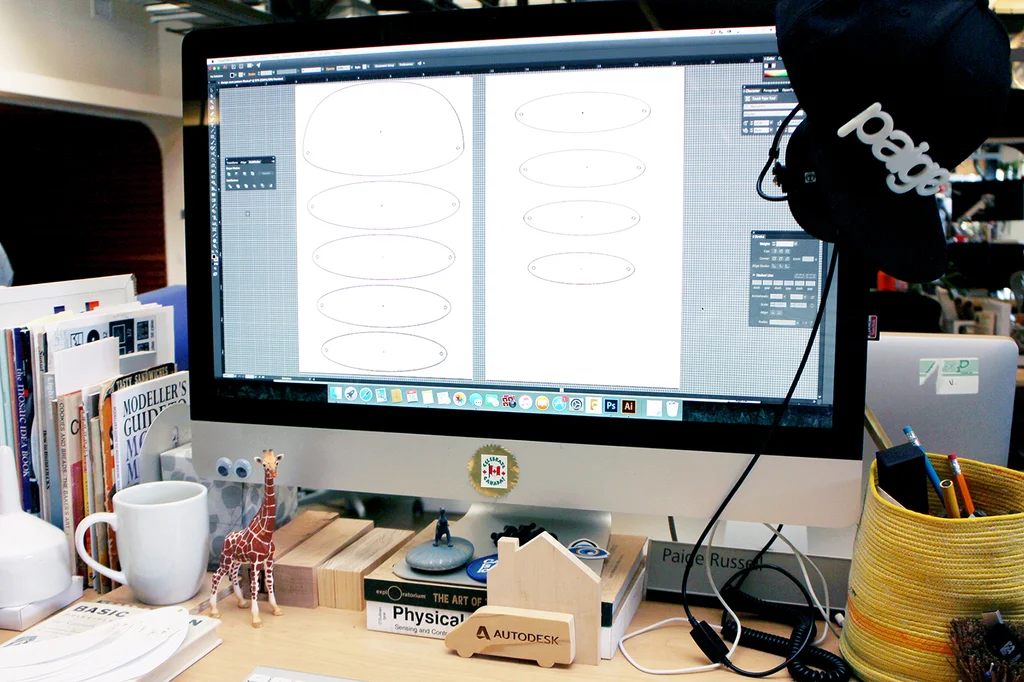
Step 2: Slicing the Model
- Use slicing software (e.g., Cura, PrusaSlicer) to divide the model into horizontal layers.
- Parameters such as layer height, infill density, support structures, and print speed are set during slicing.
- The slicer generates G-code: a set of instructions the printer can understand.
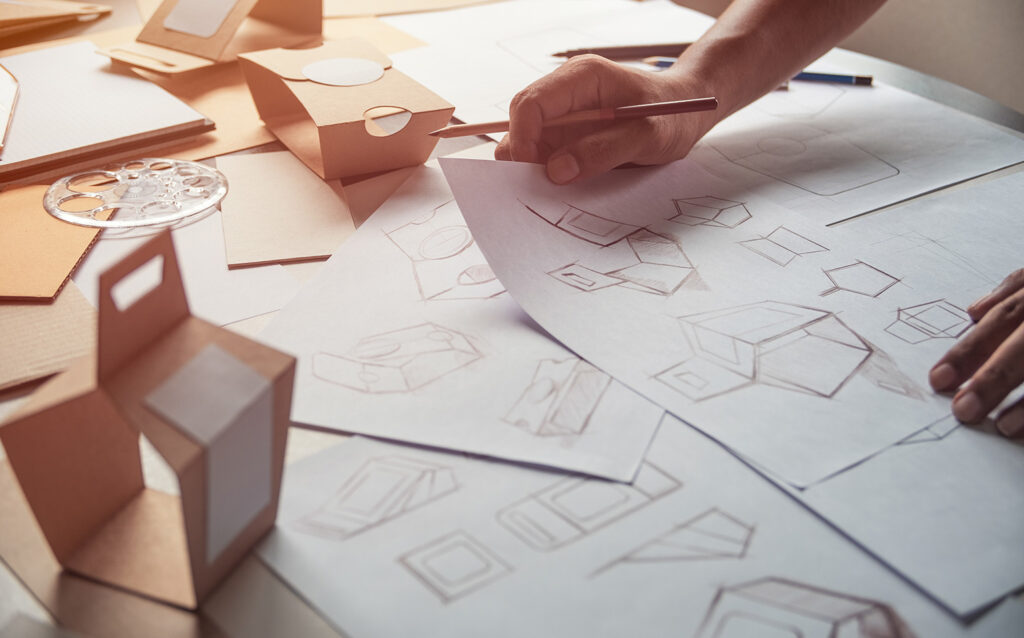
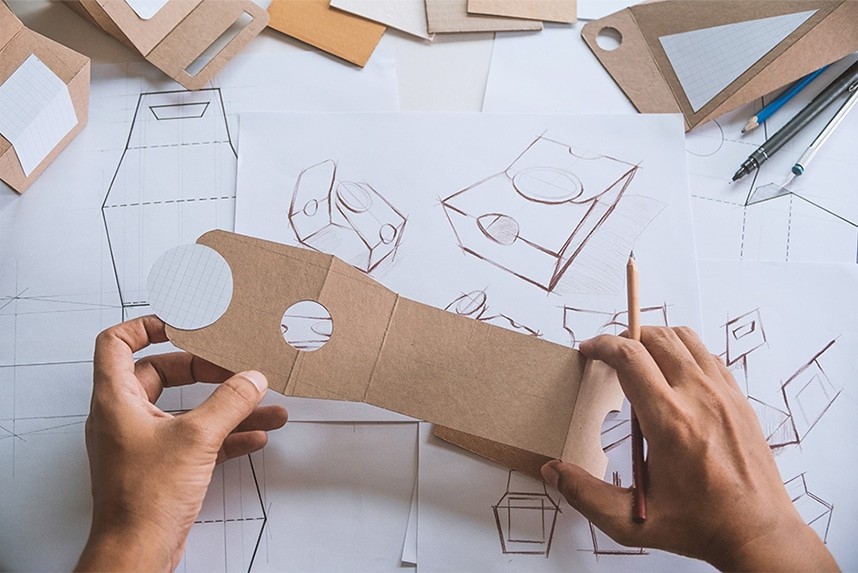
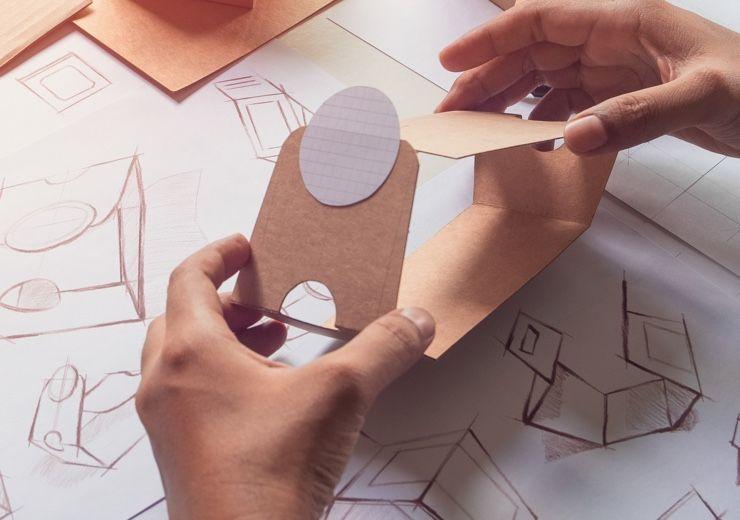
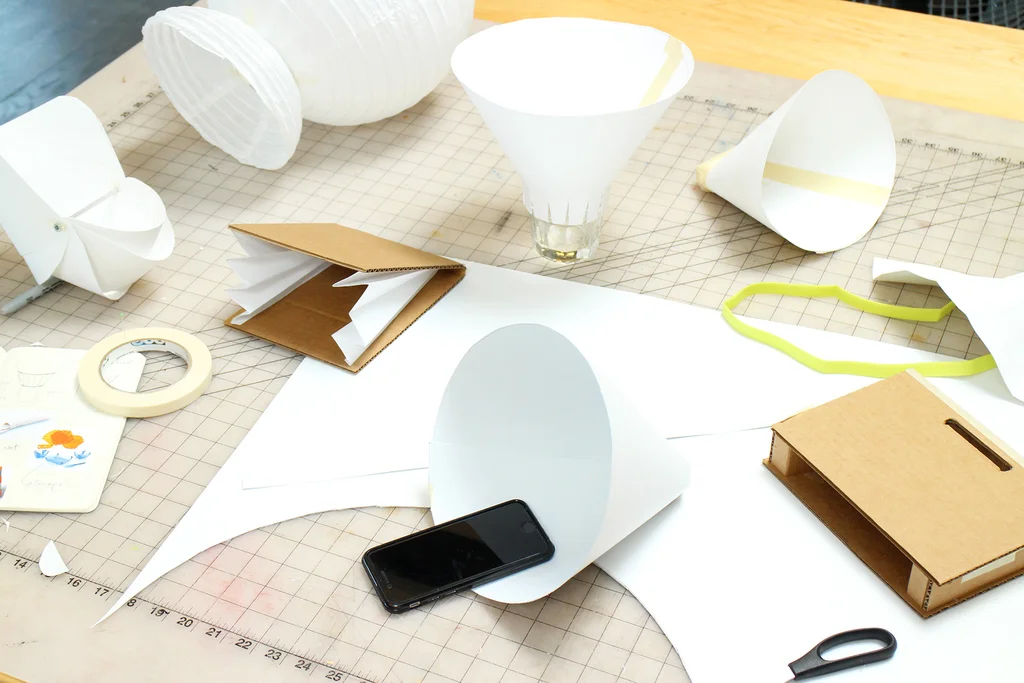
Step 3: Setting Up the Printer
- Load the appropriate material (filament, resin, or powder).
- Calibrate the build platform (leveling and positioning).
- Adjust temperature settings for the material if necessary.
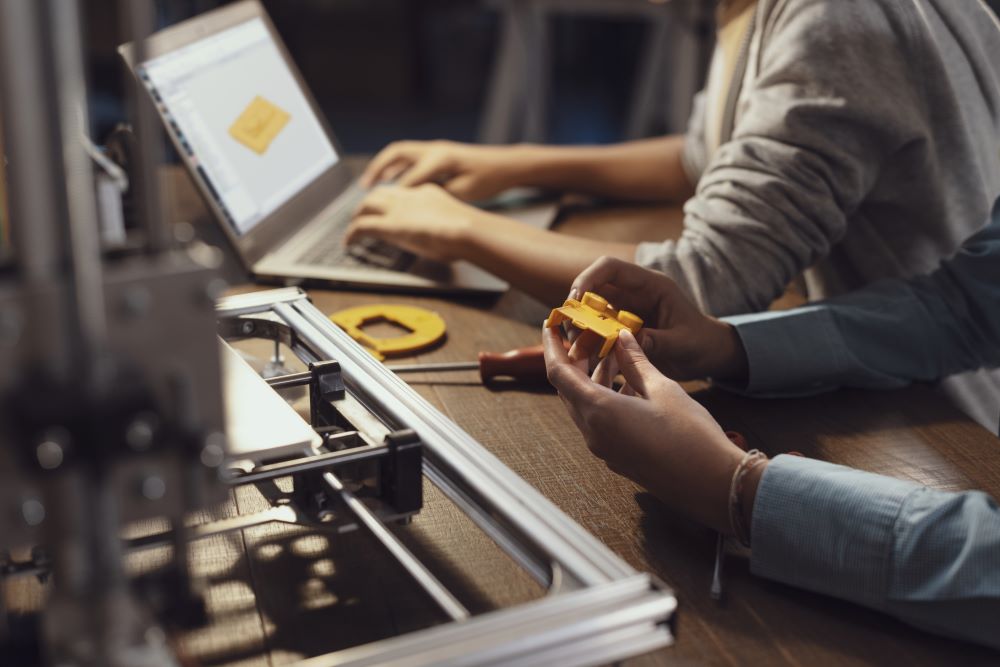
Step 4: Printing
- The printer follows the G-code instructions.
- Materials are deposited, cured, or sintered layer by layer.
- Real-time monitoring ensures the print progresses correctly (some advanced systems use cameras and sensors).
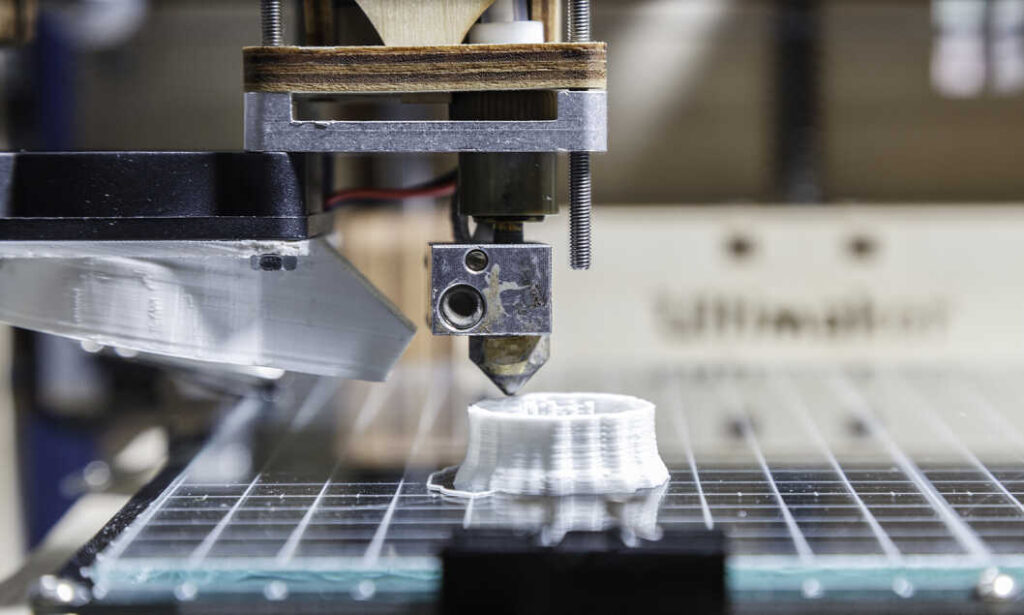
Step 5: Post-Processing
- Remove the printed object from the build platform carefully.
- Perform post-processing depending on the technology:
- FDM: Remove support material, sanding, polishing.
- SLA: Rinse in isopropyl alcohol (IPA), post-cure under UV light.
- SLS/DMLS: Remove excess powder, heat treatments.
- Surface treatments like painting, plating, or dyeing can be added for aesthetic or functional purposes.
Challenges and Limitations
Despite its incredible potential, 3D printing faces certain challenges:
- Surface Quality: FDM prints often show layer lines.
- Speed: Printing large objects can take many hours or even days.
- Material Limitations: Not all materials are printable; material properties may differ from traditionally manufactured items.
- Cost: High-end printers and materials, especially metals, are expensive.
Conclusion
3D printing technology has dramatically changed how we create objects, offering unmatched design freedom, rapid prototyping, and even customized production. By understanding the different technologies and the detailed technical processes, businesses and individuals alike can better harness the capabilities of additive manufacturing for innovation and efficiency.
As material science, machine precision, and software algorithms continue to advance, the future of 3D printing promises even more transformative possibilities — from on-demand manufacturing to building entire houses layer by layer.
More Stories
Magnetic Nanomaterials: A Revolutionary Solution for Oil Spill Cleanup
Bengaluru Teen’s Solar Innovation Powers 100 Rural Homes, Wins Global Recognition
Nikhil Kamath: The Visionary Reshaping Indian Financial Markets